プラスチックの多角的評価による品質の安定性向上
PC/ABS樹脂の配合比率による違い
PC/ABS樹脂はPC樹脂の耐熱性,耐衝撃性および易難燃化製にABS樹脂の成形加工性,メッキ特性などが付加された熱可塑性樹脂で耐衝撃性,耐候性,成型加工性を有していることから,自動車内装部品,事務機器,家電機器など幅広く使用されています。PC/ABS樹脂は組成比率を変化させることで要求仕様に合わせた特性を得ることができますが,万が一成形機に投入する配合比率に間違いが発生した場合は成形不良となってしまいます。このため,成形前の投入比率の確認だけではなく成形後の材料特性を評価して目的に沿った成形が実施されたかを確認することが重要です。今回は,配合比率を変えて成形したPC/ABS試験片についてサンプルの配合比率と各種特性の関係性を評価すると共に,配合比率と成形後の組成比率の一致性について評価しました。
内容
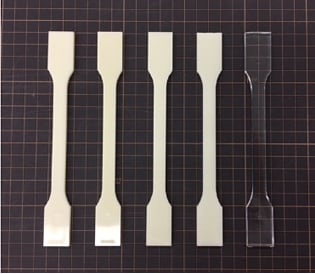
図1 サンプル外観
左からPC:ABS = 0: 100, PC:ABS = 25: 75,
PC:ABS = 50: 50,PC:ABS = 75: 25 ,
PC:ABS = 100: 0
表1 成形前の加熱条件
PC:ABS | 混錬機での混錬 | 成形機での混錬 |
---|---|---|
0:100 | なし | 220℃,約250秒 |
25:75 | 260℃,約120秒 | 260℃,約250秒 |
50:50 | 260℃,約120秒 | 260℃,約250秒 |
75:25 | 260℃,約120秒 | 260℃,約250秒 |
100:00 | なし | 290℃,約250秒 |
■ 黄色度測定:UV-2600i
ABSの比率が高まるにつれて黄色度が高いことが分かりました。
材料投入比率による材料諸特性の比較評価
材料投入比率に対し直線性が得られた材料特性値(引張強さ,PCのガラス転移点)は材料投入比率以外の影響(例:ABS中ブタジエンの熱劣化など)を受けにくかったと推察されます。一方,材料投入比率に対し直線性が得られなかった材料特性値(弾性率,HIT)は配合比率以外の影響に対して敏感に反応したと推察されます。
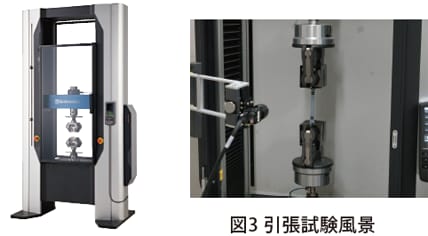
■ 引張試験:AGX-V
PCの材料投入比率が高まるにつれ引張強さが増加し,材料投入比率に対し直線性が得られました。PC:ABSが0:100から75:25は弾性率が増加しPC:ABSが100:0では減少しました。
■ 熱分析:DSC-60 plus
PCのガラス転移点と材料投入比率で直線性が得られました。
■ 硬さ試験:DUH-210
PC:ABSが0:100から75:25はHITが増加しPC:ABSが100:0では減少しました。
材料投入比率と組成比率の比較
材料投入比率と成形後の試験片の組成比率に直線性が得られました。
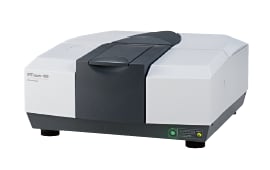
■ 組成分析:IRTracer-100
C=O結合のピーク強度と材料投入比率で直線性が得られました。
C=O結合はPCのみの官能基であるためC=O結合のピーク強度からPCとABSの組成比に換算しました。
組成比と材料特性の相関
組成比率と材料特性値に直線性が得られました。
FTIRで得られた組成比率と材料特性値を比較しました。
ここがポイント!
- 引張強さ,PCのガラス転移点,C=O結合のピーク強度のように材料投入比率に対して直線性が得られた評価手段を用いて予め既知の材料投入比率の試験片に対してデータを取得しておくことで,未知の材料に対するおおよその投入前の配合比率の確認が可能。
- 特定の材料特性の変化が必ずしも材料前の投入比率による変化を示すとは限らない。1つの管理基準で組成比率を確認するだけでは誤判断につながる可能性がある。
多角的な評価は1つの管理基準に比べて誤判断のリスク低減に有効