5.脱気方法
前項までに,移動相の脱気が必要な例を示しましたが,ここでは脱気方法を紹介します。 大別すると,オフライン脱気とオンライン脱気に分けることができます。
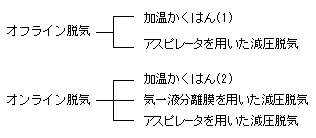
オフライン脱気は,移動相ピンをポンプ入口部にセットする前にあらかじめ脱気をしておく方法ですが,ポンプ入口部にセットした後に空気の再溶解が始まるため,脱気を充分してもあまり意味がありません。 一方,オンライン脱気は分析中に常時脱気をし続ける方法です。 取り扱いはやや手間を要しますが,分析の信頼性を高めるのに有用です。 それぞれ,長所・短所がありますので,以下に示します。
5-1)加温かくはん(1)
移動相ビン内溶液の空気溶解量を,飽和溶解量の値へ減らすために用いられます。 倉庫で冷えた溶媒を用いる際や,朝から昼にかけて室温上昇が予想される際,さらに水-アセトニトリルを混合した際は,分析中よりも移動相ビンをセットした時の方が液温が低いことになります。 そこで,少し加温して素早く平衡状態に到達させます。 液温が低いと,液体の密度も異なるわけですから,送液量にも影響します。 この影響を除く効果も目的とします。
オンライン脱気の気-液分離膜を用いた脱気や,Heパージによる脱気を行う場合も,あらかじめこの操作をしておくことが好ましいと言えます。
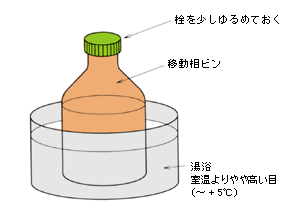
図21 加温かくはん(1)
<操作>
|
<短所> | |||||
|
|||||
<用途> | |||||
|
<操作> | |||
|
< 長所 > | ||||||
|
||||||
<短所> | ||||||
|
||||||
<用途> | ||||||
|
補足キーワード:アスピレ-ター,Aspirator,吸引器
5-3)加温かくはん(2)
オンラインで加温かくはんを行う方法です。 移動相をカラム・検出器セルの温度に保温することができるため,一定組成送液では,気泡発生もなく,屈折計ベースラインも安定になります。 移動相温度を上げるほど脱気能力は向上しますが,沸騰気泡のサクションフィルタへの進入防止や,サクションチューブやポンプヘッドの保温もしくは温調が必要になります。
|
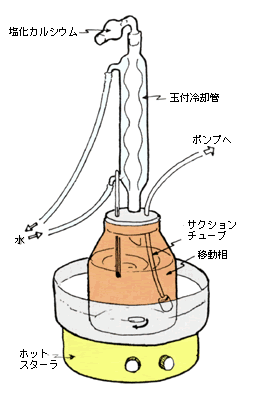
5-4)気-液分離膜を用いた減圧脱気
移動相ビンと送液ポンプの間に設置するタイプで,単に“脱気ユニット”と呼ばれるほど広く用いられています。 樹脂膜チューブの外側を減圧状態に保ち,膜の透過性を利用して,分子サイズの小さな酸素分子・窒素分子を移動相溶液から排出します。 約70~95%の空気を除くことができるため,グラジエントを含めて流路中での気泡発生によるトラブルを防止できる上,一部の高感度検出に適するようになります。
(脱気ユニット製品ページ)
<操作 > | |||||||||
|
|||||||||
< 長所 > | |||||||||
|
|||||||||
<短所> | |||||||||
|
|||||||||
<用途> | |||||||||
|
![]() |
![]() |
||
|
||
![]() |
||
![]() |
||
|
||
![]() |
||
![]() |
||
|
||
![]() |
||
![]() |
||
|
|
![]() |
||
|
||
![]() |
||
![]() |
||
|
* 本ページはLCtalk特集号5(1991年)をhtml化して一部修正を加えたものです。
従って,最新の装置情報・技術情報とは一致していない所があります。
5-5)Heパージによる脱気
移動相にHe(ヘリウム)をバブリングすると,溶解している空気が追い出されて代わりにHeが溶解することになります。Heは,図32に示したように各溶媒への溶解度がおしなべて低く,またその溶解度は図33に示したように温度の影響がわずかしかありません。従って,溶存酸素の影響が強いUV検出や蛍光検出は勿論,屈折計においても高感度で安定したベースラインが得られます。本法は,Heパージ,あるいはHeガスバブリング,スパージ(sparge)などと呼ばれています。
ただし,移動相ビン中でHeパージをしても,ビンが開放になっている状態(図36)では,逆に余計ベースラインが安定しない場合があります。何故なら,接液気体に常に空気が含まれることになり,空気の完全な追い出しが不可能になるからです。さらに,He流量を変えると空気の分圧も変動し,ベースラインドリフトが生じることになります。 従って,Heパージをする場合は,できるだけ密閉加圧式で行うことが望ましいと言えます。
(脱気ユニット製品ページ)
<操作>
密閉加圧式のHeパージは,図35のような流路が必要となる。注意点は移動相ビンのキャップに専用の密閉キャップ(DGU-10Aなどには標準付属品として含まれる)を用いることである。まず,初期にHe流量を上げて(圧力で調整する。例えば 0.02~0.05MPa =0.2~0.5kgfcm-2)10~30分流し,移動相中から空気を追い出す。次に排気バルブを閉じると,接液気体は少し加圧された状態となる。この時点で移動相は「分析に使える」状態になる。以後,ポンプの送液により移動相が減った分だけ,Heガスが供給されることになる。
分析終了時は,排気バルブを開けた後,調圧弁の圧力をゼロにするか,INバルブがあればそれをOFFにする。このとき,He OUTチューブを通してHeが徐々に抜けるために(空気は入りにくくチューブ内が減圧になり),He OUTフィルタから移動相が逆流することがある。リーク用抵抗管がユニット内にあれば,空気が逆流することにより,この問題を防止できるが,これが無い場合はHe OUTチューブとユニットの接続部を緩めて空気を導入する。
また,ユニット内のリリーフバルブは,調圧弁がこわれた場合や,高い圧力に設定し過ぎた場合,Heを逃がして移動相ビンに過剰な圧力がかかることを防止する。勿論,より安全性を高めるため,移動相ビンにもシートやネットを巻いて安全対策する(図37)ことが好ましい(シートやネットはDGU-10Aの標準付属品に含まれる)。
なお,溶媒ガストラップは,移動相中の揮発性溶媒蒸気が室内に拡散するのを防ぐために用いるが,密閉加圧式でないHeパージの場合に,接液気体の圧力を一定に近づけるのに役立つ。
<長所>
- 脱気能力は最も優れている。
- 脱気能力の送液流量依存性はない。
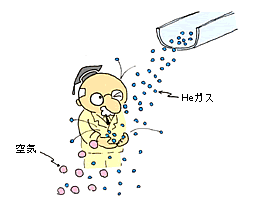
図34 Heパージのイメージ
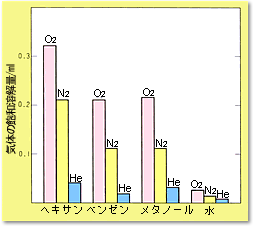
図32 溶媒1mlに対する気体の溶解量(分圧1atm,25℃)
* 1気圧(1atm) = 1.013×105Pa
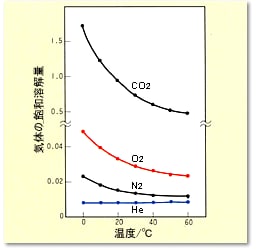
図33 水1mlに対するCO2,O2,N2,He溶解量への温度影響
(気体分圧1atm)
<短所>
- Heガスボンベ・レギュレータ・配管が必要となる。
- 密閉加圧式でないと,ベースライン安定性が保てない場合があるため,移動相ビンの口径・形状に制限がある。
- 揮発性溶媒を含む移動相を脱気する際には,溶媒組成が変化することがある。(密閉加圧式で定常状態に入った後は,組成変化は起こりにくい)
<用途>
- UV検出をはじめとする各種検出での高感度検出(密閉加圧式の場合。なお,開放系の場合は,蛍光検出・電気伝導度検出・電気化学検出での高感度検出)。
- 低圧・高圧混合グラジエントを用いた分析(それぞれの移動相ビンに単一溶媒を入れる場合は,高精度分析が可能)。
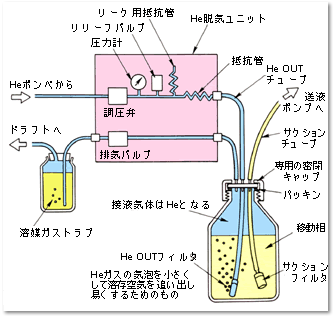
図35 Heパージによる脱気(密閉加圧式)
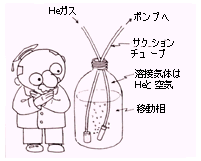
図36 「ビンの口開放でのHeパージはnot good!」
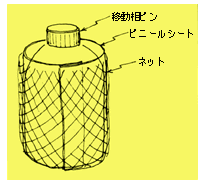
図37 密閉加圧器式の移動相ピンの安全対策
ところで,Heパージのランニングコストは,方式の違い(例えば密閉加圧式か開放式か)や,使用法,機種の違いによって大きく異なりますが,例を示しておきます。
<DGU-10A(密閉加圧式,全4流路)のランニングコスト計算例>
(条件;2流路のみ使用,移動相1Lビン×2,1日20時間運転,He圧力0.3kgfcm-2,初期パージ20分,He(99.995%)ボンベ7m3=15000円*)
- 初期パージ 300mL/min×20min×2=12L
- 定常状態 10mL/min(リーク流量)×1200min=12L
- 移動相減少分補給 約2L
トータル1日当り約26L(56円)
*Heボンベ7m3の市価は7000~20000円と幅がある。
* 本ページはLCtalk特集号5(1991年)をhtml化して一部修正を加えたものです。
従って,最新の装置情報・技術情報とは一致していない所があります。
|
![]() |
||||||||||
|
||||||||||
![]() |
||||||||||
|
* 本ページはLCtalk特集号5(1991年)をhtml化して一部修正を加えたものです。
従って,最新の装置情報・技術情報とは一致していない所があります。