3.流路中での気泡発生によるトラブル
それでは,1.項で示した流路中での気泡発生によるトラブルについて,2.項のメカニズムを念頭において見直してみることにしましょう。
3-1)移動相ビン内での気泡発生による送液トラブル
移動相ビン内で気泡発生する場合は,その移動相中の溶存空気が過飽和の状態であることを示します。 例えば,次のようなことが考えられます。
- (1) 液温上昇 ・・・・・・倉庫で冷えていた溶媒をすぐに移動相ビンに入れて暖かい室温で用いたり,朝に移動相をセットしたが昼になって室温が上がった場合です。
- (2) 混合溶媒のかくはん不足 ・・・・・・特に,水-アセトニトリルを混合すると吸熱反応で液温が下がります。 従って充分かくはんして過飽和な空気を除いたつもりでも,室温で暖められ,液温が上がるにつれて気泡発生することになります。
これらの気泡がサクションフィルタ・チューブを経てポンプヘッドに吸い込まれると,送液が正常でなくなります。まず,吸引時には,ヘッド内部がやや減圧になるために気泡が膨張します(図8)。このときプランジャは,膨張した気泡を含めて吸引容量の計量を行うことになります。 次に吐出時には,ヘッド内部が高圧になるため気泡が収縮します。 従って,送液される移動相量は正常時よりも小さくなります。このように,ヘッド内を気泡が不規則に通過することは,送液する移動相量が不規則になる(送液正確度・精度不良)ことを意味します。なお,この現象の有無は,送液ポンプの吐出圧力波形をモニタ(図9)すれば判ります。
このような問題が起こった場合,ピークの保持時間・面積値にバラツキが生じやすくなり(図10),分析の信頼性に欠けるようになります。
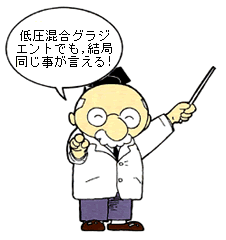
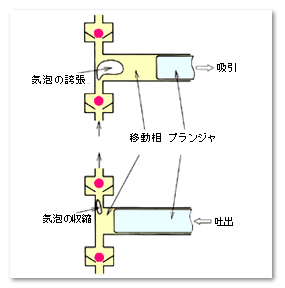
図8 気泡が入ったポンプヘッドの模式図
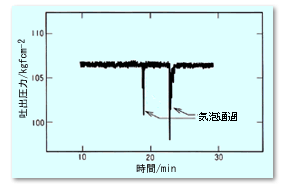
図9 吐出圧力波形の変化
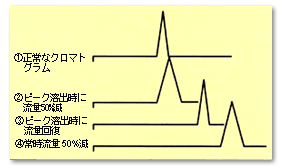
図10 送液量の不規則化によるクロマトグラム変化例
3-2)ポンプ内での気泡発生による送液不良
移動相ビン内の溶液に溶解している空気が飽和溶解量以下であっても,ポンプを通過する際に気泡が発生することがあります。
(1)低圧混合グラジエント ・・・・・・異なる溶媒を大気圧(もしくはやや減圧)下で混合するため,メカニズム2-3)により,図11中赤ワクの所で気泡が発生します。 いくらグラジエントミキサがポンプ下流(高圧側)に設置してあっても,図中赤ワクの所ですでに混合が始まるので,多かれ少なかれ気泡発生が起こります。一方,高圧混合グラジエントの場合は,混合が始まる所がポンプ下流(高圧側)であるので,この問題は起こりません。
(2)サクションフィルタの目詰まり ・・・・・・サクションフィルタが目詰まりしていると,吸引時の抵抗が大きく,フィルタ内部が減圧になって気泡が発生しやすくなります。目詰まりは,フィルタの放置によりゴミが付着したり,前の移動相が緩衝液であることを知らずにメタノールを流すことなどにより起こります。なお,目詰まりが軽度であれば,移動相の充分な脱気により気泡発生を防止できますが,これは本来は,フィルタの洗浄や交換によって解決すべき問題です。
これらによって発生するトラブルは3-1)の場合と同じです。
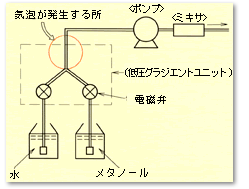
図11 低圧混合グラジエント
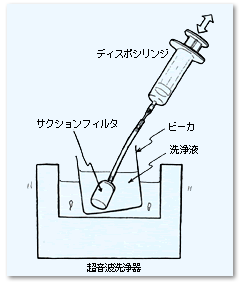
図12 サクションフィルダの洗浄
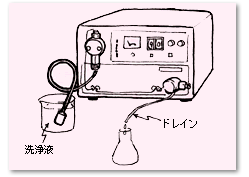
図13 サクションフィルタの洗浄
ちょっと道草
サクションフィルタの洗浄法
サクションフィルタに不溶性物・ゴミが詰まった場合は,図12のように超音波洗浄器中で逆洗を試みてみましょう。化合物の析出であれば,洗浄液を水→A→イソプロピルアルコール→クロロホルム(A;酸性有機化合物なら希アンモニア水/メタノール,塩基性有機化合物なら希りん酸水/メタノール)に切り替えて洗います。さらにポンプを使って充分洗浄してみましょう(図13)。洗浄後も大流速時にサクションチューブに気泡が見える場合は交換して下さい。
なお,洗浄液として金属粉に対しては希硝酸(アルコールと触れないようにして下さい)を,金属イオンにはEDTA・-2Na水を,たんぱくにはSDS水溶液を用いることが多いようです。
一般にカラム内では圧力がかかっているため,空気の飽和溶解度が上がっており,気泡は発生しにくいはずです。 しかし,カラム出口付近の比較的圧力の低い部分では,オーブンで加温されていると気泡が発生しやすくなります。 また,ポンプを素通りしてきた気泡が滞留することも考えられます。
このような場合には,カラム内での移動相の流れは一様でなくなり,結果的にピーク変形が起こる場合があります(図14)。
なお,カラムからの気泡の抜けにくさは,大口径カラムほど顕著になります。 従って分取用カラムをHPLCに取り付ける場合は,少しでも気泡が浮力に逆らわなくて済むように入口側を下に出口側を上に取り付けることをおすすめします。
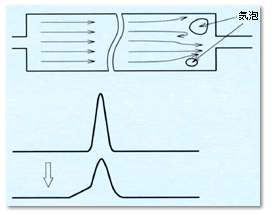
図14 カラム内気泡によるチャンネリング
カラム,あるいは検出器セル部が加温されている場合,セルを通過する液温は上昇しており,圧力も大気圧に近い状態であることから気泡が発生しやすくなっています。また,加温されていなくてもグラジエントの場合は気泡が発生することがあります。溶媒を混合すると飽和溶解度が低下することは2-3)で述べた通りです。例えば,高圧混合グラジエントの場合,混合後流路中で常時高圧下のため気泡発生が抑制されるのですが,セル内は大気圧に近く気泡発生が起こります。
このような,セル内での気泡発生や滞留は,図15のようなスパイク状・ノコギリ状のノイズを引き起こしたり,ベースラインを振り切ったりします。この結果,ピークとノイズの区別ができなかったり,ベースライン位置が不明確になったりして,波形処理(面積計算)が正しく行われなくなります。
なお,3-3),3-4)のケースとも,検出器がUV検出器や電気伝導検出器であれば,セル耐圧が高いため(12MPa,3MPa),検出器出口側に背圧をかけてカラム出口やセル内にかかる圧力を高め,気泡発生を防止できます。通常,背圧には0.3mm内径×2m長さのステンレスチューブを抵抗管として接続します。水,メタノールを1mL/minで送液するとそれぞれ約0.2,0.1MPa圧力が生じます。溶媒の種類により圧力が異なるのは次式に示すように溶媒粘性が効くためです。
〔圧力〕∝〔溶媒粘度〕〔流速〕〔チューブ長さ〕(但し,チューブ内径一定で層流のとき)
なお分取流量で使用の場合は,同じ抵抗管では圧力がかかり過ぎるため,チューブを短くするか,内径の大きなチューブ(例えば0.8mm内径)を使って下さい。一方,セミミクロLCなど流量が低い場合は(例えば0.1mL/min),同じ抵抗管では圧力がかかりにくくなるため,0.2mm内径×6m長さのチューブなど背圧のかかりやすいものに変える必要があります。
* 1MPa=10.2kgf/cm21kgf/cm2= 0.098MPa
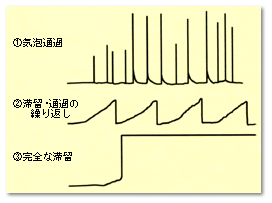
図15 セル内での気泡発生・滞留によるベースラインノイズ
検出器の種類 | 耐圧 MPa,(kgfcm-2) |
---|---|
UV(VIS)検出器 | ~12,(120) |
電気伝導度検出器 | ~3,(30) |
蛍光検出器 | ~0.5,(5) |
示差屈折計検出器 | ~0.4,(4)* |
電気化学検出器 | ~0** |
*電気弁耐圧 セル耐圧は2MPaまで
**Ag/Agcl参照電極を用いるとき
ただし,電気化学検出器の場合は,セル耐圧が低いために背圧をかけられません。このような場合は,あらかじめ移動相中の空気を脱気しておくことが必要です。
以上,流路中の気泡発生によるトラブルを見直してきましたが,ポイントはやはり温度上昇・圧力降下・溶媒混合です。図16に流路と圧力・温度の関係の例を示しましたので,みなさんのシステムではどの部分で発生の可能性が高いかを考えてみて下さい。
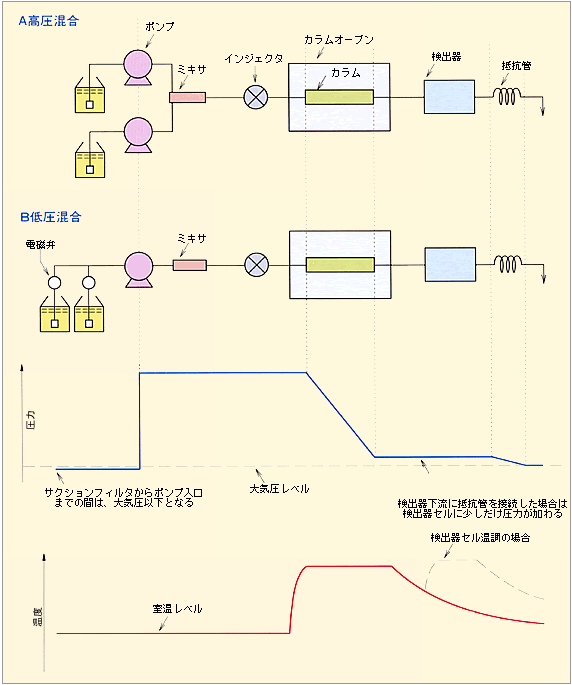
図16 セル内での気泡発生・滞留によるベースラインノイズ
* 本ページはLCtalk特集号5(1991年)をhtml化して一部修正を加えたものです。
従って,最新の装置情報・技術情報とは一致していない所があります。